Building specifications are the backbone of any successful project in the construction industry, providing detailed instructions that guide the entire process from concept to completion. Understanding these technical documents can seem daunting for beginners in the field, but understanding specifications is essential to ensure that every building aspect meets the required standards.
This guide breaks down the basics of building specifications, covering what they are, their key components, and their critical role in construction. Whether you’re new to the industry or looking to refine your knowledge, this guide will help you navigate the process of writing building specifications and tackling common challenges.
What are building specifications?
Building specifications, often called buildspec, are detailed documents that outline the materials, products, standards, workmanship, and construction techniques required for a building project. They work alongside architectural drawings to describe what is needed to bring a project to life, ensuring the work meets the required quality and compliance standards.
Specifications detail various aspects of the project, such as:
- Materials: Types, grades, and sources of materials to be used, including finishes, fixtures, and fittings.
- Workmanship: Standards for installing or applying materials, including specific methods or techniques to ensure quality.
- Quality standards: Industry or local standards that the project must adhere to, ensuring safety, durability, and compliance with regulations.
- Performance requirements: Materials and installations must meet technical criteria, such as insulation values or structural loads.
Building specifications serve as a reference for contractors, engineers, and architects, helping ensure consistency and reducing the likelihood of misunderstandings or disputes during construction.
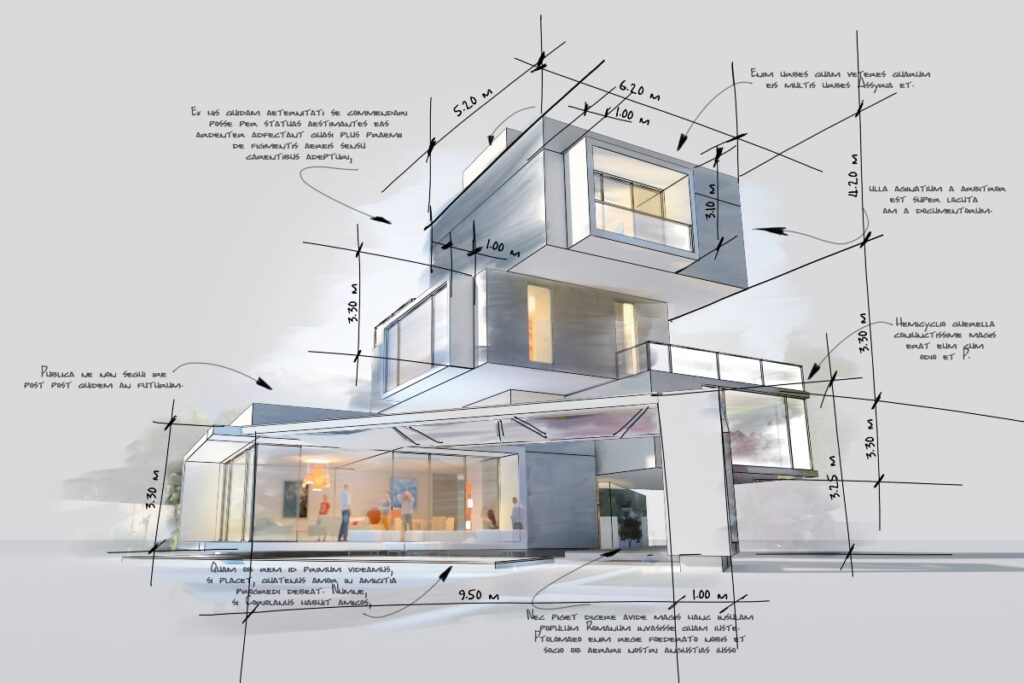
Critical components of building specifications
Construction project engineers rely on detailed specifications to ensure that all components, from materials to installation procedures, meet the project’s requirements. Construction specifications ensure clarity, consistency, and quality in construction through several key components:
- General requirements: Defines scope, project timeline, site access, contractor requirements, quality control, and regulatory compliance.
- Materials and products: Details all materials, products, and systems, specifying types, grades, and sources to ensure consistency.
- Workmanship standards: Sets quality expectations and installation methods, ensuring consistent application of materials.
- Performance specifications: A performance specification outlines technical standards, such as insulation values, energy efficiency, and load capacities.
- Execution and installation procedures: Provides step-by-step instructions for proper assembly and installation.
- Testing and quality assurance: Includes criteria for inspections and tests to ensure compliance with Australian standards.
- References to standards and codes: Lists relevant industry standards and regulations, ensuring legal compliance.
- Schedules: Details timelines for materials, fixtures, and deliveries to coordinate project progress.
These elements work together to define all aspects of a project, maintaining quality and reducing risks throughout the construction process.
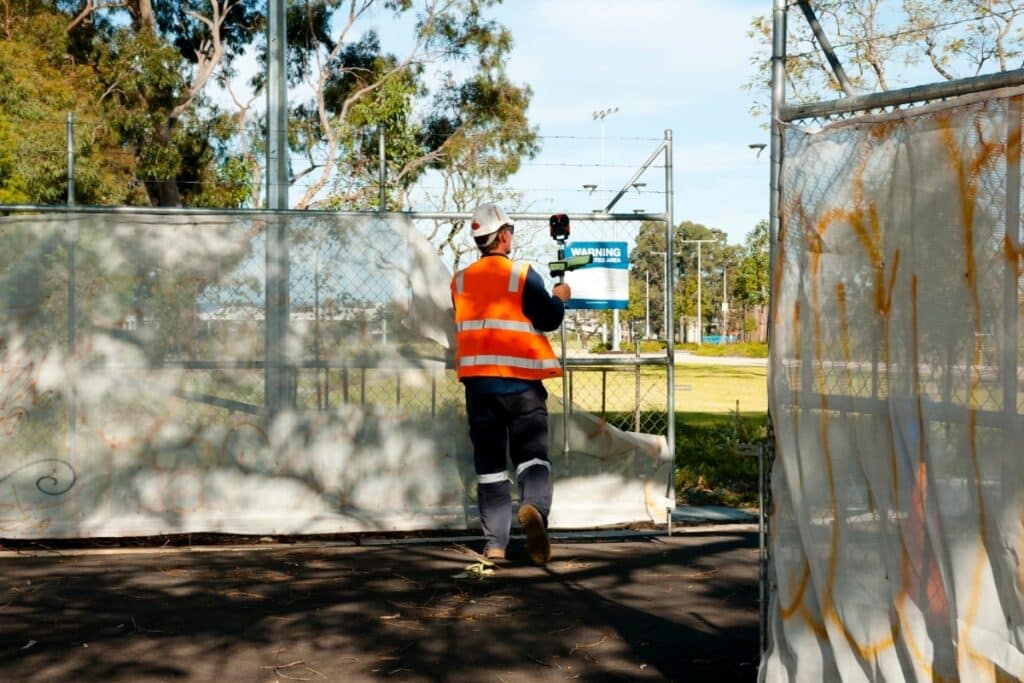
The role of building specifications in construction
Construction specifications are essential in guiding construction projects, acting as a blueprint that ensures materials, methods, and workmanship align with design standards. Their key roles include:
- Setting clear expectations: Specifications detail materials and quality standards, reducing misunderstandings and keeping the project on track.
- Ensuring compliance: They integrate building codes and regulations for using safety equipment, ensuring legal standards are met for a safe structure.
- Quality control: Specifications provide benchmarks for assessing work quality, helping to identify and resolve issues early.
- Managing costs: Outlining materials and methods prevents unplanned changes, aiding in accurate budgeting.
- Improving communication: As a reference, construction specifications align architects, contractors, and clients, fostering collaboration.
- Minimising disputes: Clear guidelines reduce disagreements and delays by defining what’s required.
- Adapting to changes: Specifications can include contingencies for material shortages or site conditions, offering flexibility.
In the early stages of building, specifications help establish clear expectations and align the design vision with practical construction requirements.
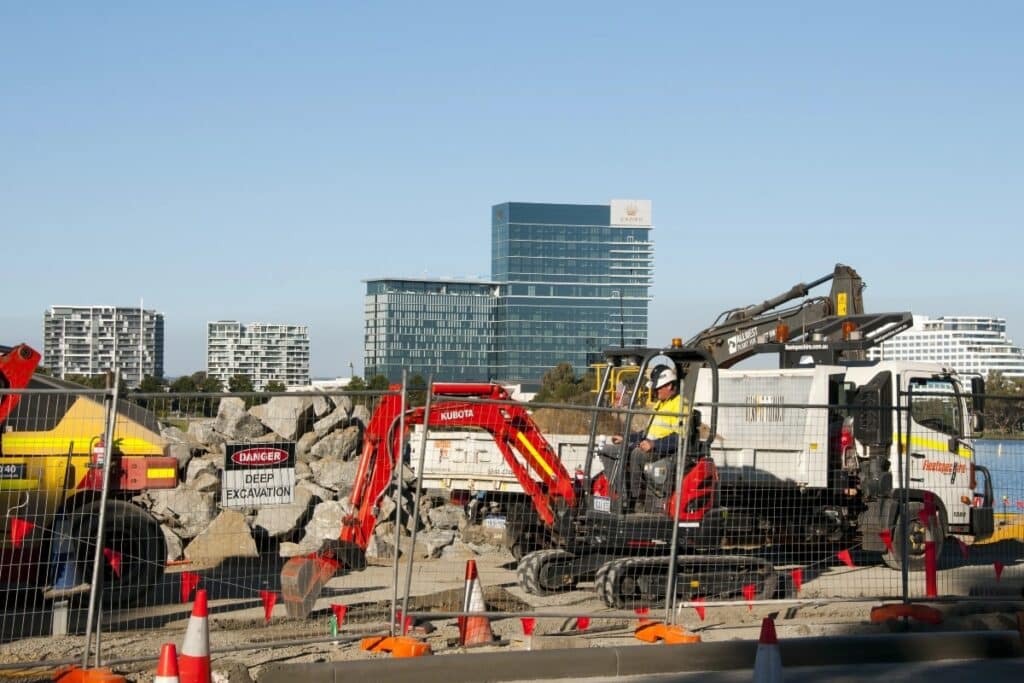
How to write effective building specifications
Writing clear and precise specifications can significantly impact a project’s development, ensuring that all phases progress smoothly and according to plan. Follow these steps for specification writing:
- Understand the project: Align specifications with the project’s goals and client needs.
- Be clear and concise: Use straightforward language to avoid misunderstandings.
- Reference standards: Include relevant industry standards, codes, and regulations.
- Detail materials: Proprietary specifications such as exact product types, brands, and material performance criteria.
- Define quality: Set clear benchmarks for workmanship and performance.
- Include installation methods: Provide instructions to ensure consistent construction specs.
- Plan for testing: Outline procedures for inspections and quality checks.
- Anticipate challenges: Offer guidance for handling issues like material substitutions.
- Review and update: Regularly revise specifications to reflect project changes.
These steps help create precise specifications, ensuring quality and compliance throughout the project.
Common challenges in building specifications
Specifications are essential for successful construction, but they can present challenges. Here are some common issues:
- Ambiguity and misinterpretation: Vague language can cause misunderstandings about materials, methods, or quality standards, leading to delays or conflicts.
- Keeping up with changing regulations: Frequent updates to building codes require specifications to be revised, which can be time-consuming.
- Material availability and substitutions: Supply chain issues may require substitutions, which must still meet original performance standards.
- Balancing detail with flexibility: Overly rigid specs limit flexibility, while too little detail causes inconsistencies—striking the right balance is key.
- Coordination among stakeholders: Aligning input from architects, engineers, and contractors is complex and can lead to conflicts or delays.
- Cost control: Errors or omissions in specs can lead to budget overruns; specifying alternatives can help manage costs.
- Quality assurance and verification: Ensuring that work meets specifications requires thorough inspections and testing, which can be challenging to manage.
Addressing these challenges requires clear communication, attention to detail, and regular reviews to ensure specifications remain accurate and practical throughout the building project.
The future of building specifications
The future of building specifications is shaped by evolving technology, sustainability, and industry standards. Here are key trends to watch:
- Digital transformation: The adoption of Building Information Modelling (BIM) and digital platforms makes specifications more interactive, integrating them with 3D models for better visualisation and collaboration.
- Sustainability focus: Specifications increasingly incorporate green building standards and sustainable materials, responding to the demand for eco-friendly construction practices.
- Automation and AI: AI-driven tools are beginning to assist in writing specifications, automating repetitive tasks, ensuring accuracy, and identifying potential errors early in the process.
- Enhanced collaboration: Cloud-based platforms enable real-time updates and collaboration among architects, engineers, and contractors, improving the alignment of specifications across the project.
- Performance-based specifications: A growing trend toward using performance specifications allows for more significant innovation and adaptability in meeting construction goals.
- Standardisation of data: Efforts are being made to standardise specification formats and data structures, making it easier to share and integrate specifications across different software and projects.
- Focus on resilience: As climate change impacts building design, specifications adapt to include resilience measures, such as materials and methods that enhance durability and withstand extreme weather conditions.
These trends are making construction specifications more efficient, adaptive, and aligned with modern construction needs, helping to drive quality and innovation in the industry.
Fencing solutions for the construction industry
For high-quality temporary fencing, barriers, and site accessories, contact TTFS. Our products are built for durability and strength and are designed to meet your specific requirements. Explore our extensive range of products to keep your site secure.
Contact our experienced team today by calling 1300 119 998 or completing an enquiry form.
FAQs
Here are three FAQs for the article on building specifications:
What are building specifications, and why are they important?
Building specifications outline the materials, standards, and methods required for a construction project. They ensure that all aspects of a build align with quality and compliance standards, reducing misunderstandings and helping to achieve a successful outcome.
How do building specifications help in managing construction costs?
Specifications prevent cost overruns by clearly defining materials, methods, and standards. This allows for more accurate budgeting, reduces the need for unplanned changes, and ensures that contractors can provide precise quotes.
What challenges are commonly faced when creating building specifications?
Common challenges include keeping up with changing regulations, managing material availability, balancing detail with flexibility, and ensuring quality through thorough inspections. Addressing these requires clear communication and regular updates to the specifications.